Corrective Action vs. Preventive Action
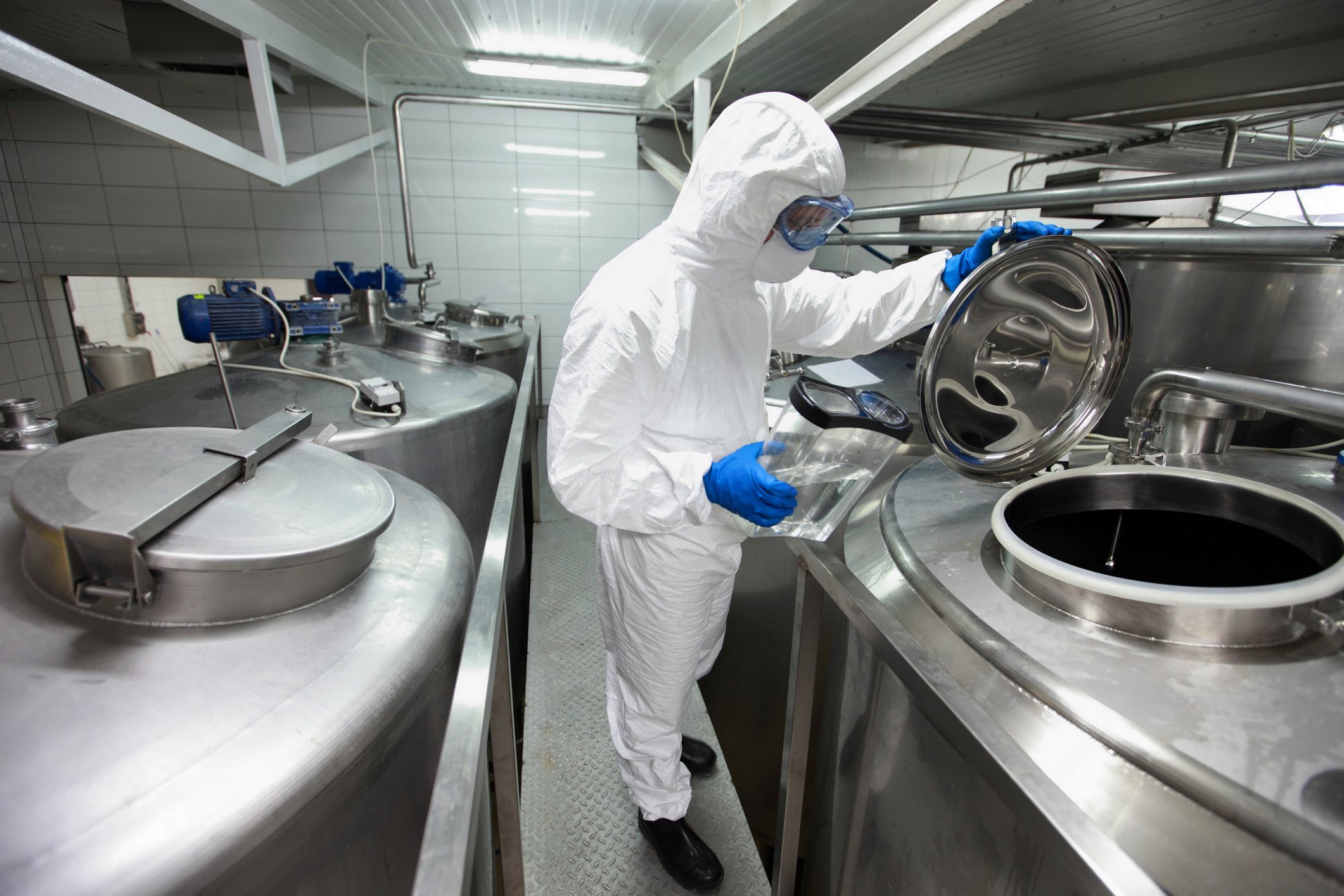
When implementing a management system, there can be some confusion in terminology. Two terms that are often misunderstood are corrective action and preventive action. At a glance, they can be mistaken as similar terms; however, they mean very different things and serve different purposes within the operation of a management system.
Corrective Action
ISO 9000 defines corrective action as:
“action to eliminate the cause of a nonconformity and to prevent recurrence”
ISO 9000:2015, 3.12.2
“Eliminate” being the key word, this definition shows that corrective action happens after the nonconformity exists. Corrective action corrects a nonconformity and should ensure that it does not recur by eliminating the cause of the nonconformity.
Plan-Do-Check-Act (PDCA) in ISO 9001 is a beneficial tool that complements corrective action and allows for continual improvement. Ishikawa diagrams, five whys, and Pareto charts aid in determining the cause of the nonconformity so corrective actions can be planned accordingly.
Preventive Action
ISO 9000 defines preventive action as:
“action to eliminate the cause of a potential nonconformity or other potential undesirable situation”
ISO 9000:2015, 3.12.1
In this case, action is taken so that potential nonconformities do not happen in the first place. It is a proactive approach to continual improvement.
Preventive action allows organizations to explore risks and opportunities that can potentially benefit the organization. When used in risk-based thinking, preventive action allows for growth, as opportunities can be fully considered and risks can be controlled, where needed. With proactive planning, preventive action allows organizations to achieve the best outcomes. Tools such as checklists or FMEA (Failure Mode and Effects Analysis) can help with the implementation of preventive actions.
Risk-Based Thinking
Continual improvement is one of the essential purposes of any management system. This means using both corrective and preventive action to analyze and prevent the reoccurrence of nonconformities that do occur, as well as prevent potential nonconformities from occurring. The combination of corrective and preventive action is considered risk-based thinking. Making sure that risks and opportunities are addressed can be incredibly beneficial for achieving greater efficiency and leads to continual improvement. Taking a risk-based thinking approach can not only eliminate waste and improve productivity, but it also opens up the organization to new opportunities that can attract new customers, develop new products or services, and more.
Both corrective and preventive action can be applied to many different industries and organizations. Using risk-based thinking can be helpful for organizations offering products or services, as well as laboratories that conduct tests and measurements.
Corrective and preventative action are both necessary for continual improvement that will ultimately make the organization more successful and efficient. If you are looking to improve your risk-based thinking skills, check out ANAB’s instructor-led course Risk-Based Thinking for Forensic Service Providers or ANAB’s self-paced course Approaches to Risk-Based Thinking in Laboratories. To learn more about the corrective action process and analysis techniques, check out ANAB’s course on The Corrective Action Process and Cause Analysis for Forensic Service Providers or ANAB’s self-paced course Cause Analysis and Corrective Action.