The Anatomy of a Laboratory Assessment
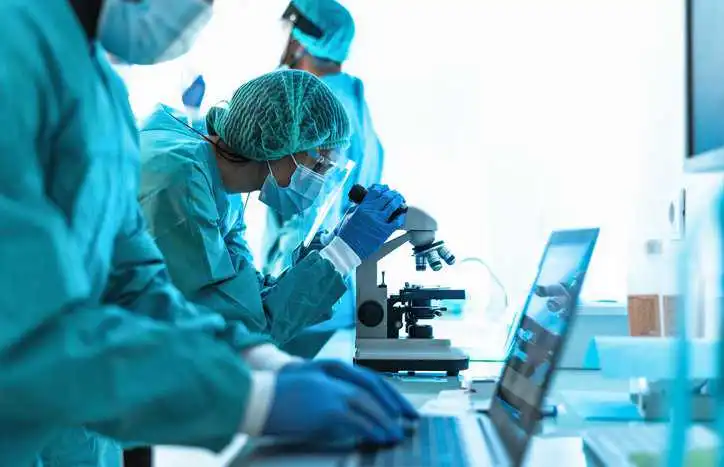
An assessment is a demonstration by a body that specified requirements are fulfilled. Assessments are performed by technically competent assessors who evaluate the competence of a laboratory for a defined scope of accreditation. Third party audits include assessments performed by representatives of an accreditation body. The term “audit” is changed to “assessment” for technical standards, such as ISO/IEC 17025, ISO/IEC 17043, and ISO 15189, because their purpose is to assess the technical competence of the laboratory.
The Laboratory Assessment Process
The typical activities performed as part of the laboratory assessment process are:
1. Preparation of an assessment activity plan
Every assessment activity requires an assessment activity plan. It is prepared by the lead assessor and clearly describes the requirements that will be assessed including the accreditation standard, accreditation requirements, and supplemental or technical requirements. The plan will detail the assessment activities that the assessor will perform including, but is not limited to, locations to be visited (including sites where key activities are performed), quality system review, technical evaluation of the scope, review and effectiveness of the prior years’ corrective actions, and special instructions.
2. Document review
The assessor performs a document review at the start of any assessment activity. Customer documentation is provided to the lead assessor for review prior to the onsite/remote assessment. This review helps the assessor prepare for the assessment activity and can identify potential areas of concern with the customer’s documentation that will be reviewed during the onsite/remote assessment.
The document review includes an evaluation of the documents for conformance with
requirements, an evaluation of the scope of accreditation, a review of management review and
internal audit results, as well as a review of PT/ILC plans and results, and other
quality and technical documentation provided by the customer.
3. On-site or remote assessment
The on-site or remote assessment consists of two main components: Management system review and technical evaluation of the scope.
Management system review: The accreditation requirements guide the assessor during the assessment. The assessor analyzes all relevant information and evidence gathered to determine the extent of competence and conformity with the specified requirements. The assessor reviews documentation and records, interviews staff, and assures objective evidence supports implementation of the management system and fulfillment of requirements. Assessors will use checklists and other records to allow for notation of conformity or nonconformity to requirements, as well as any opportunities for improvement to assure sufficient detail for the accreditation body to make an accreditation decision.
Technical evaluation of the scope: Involves a technical evaluation of the performance of a representative number of staff to provide assurance of the technical competence of the laboratory for the defined scope of accreditation. The assessor will assure methods used on the scope are valid or have been validated and will observe staff performing methods to confirm conformity with requirements and demonstration of technical competence. The assessor will interview staff, review procedures and supporting documentation, and inspect equipment used to perform the method.
4. Issuing nonconformities, if applicable
One aspect of the assessment is to ensure that the laboratory’s management system is compliant with the accreditation standard, general accreditation requirements, program-specific and regulatory requirements. Laboratory staff must demonstrate an understanding of and follow their procedures; additionally, the second aspect of the assessment is the determination of competence of staff and the technical validity of operations. Issuing nonconformities requires the professional judgment of assessors and experts. Where key personnel or other technical staff are considered not competent or where the validity of the quality management and technical operations does not meet requirements, a nonconformity with one or more elements of the accreditation requirements must be issued.
A nonconformity is defined as a “non-fulfilment of a requirement” and may include but is not limited to the following: Documentation, including records not conforming with the requirements of the standard and regulation; Staff not following documented procedure; Technician/analyst, technical managers, other key staff not demonstrating competence in the work they are doing; Operational procedures such as test or measurement methods, traceability, etc., lacking technical validity; A breakdown in the operation of the quality management system of the customer; The laboratory not conforming to accreditation body requirements.
The assessor discusses any nonconformities with the laboratory at the time they are discovered so that the laboratory can discuss any concerns or ask questions they may have prior to the ending of the assessment. At a minimum, written nonconformities consist of a statement of the requirement, a statement of the condition observed, and a reference to the evidence that supports the comparison of the requirement and the condition observed.
5. Reporting results
There are several mechanisms for reporting assessment results. The lead assessor holds a closing meeting with the laboratory to discuss the assessment activities performed, any nonconformities and opportunities for improvements, and positive findings. Additionally, the lead assessor prepares specific assessment documentation for submission to the accreditation body, including, but not limited to, an assessment summary report, summary of nonconformity, completed checklists, and completed method witnessing forms. These documents become part of the assessment package.
6. Corrective action review
The laboratory is required to provide corrective action responses for each nonconformity using their own corrective action procedures. The lead assessor reviews the responses and provides a recommendation to the accreditation body if the responses are acceptable or not. Each response must have a documented cause determined through cause analysis, corrective actions to address the cause, and evidence that corrective action has been taken. The lead assessor may ask the laboratory for additional information or documentation as part of the assessor corrective action review process. Once all responses are accepted by the assessor, the corrective actions and review comments from the assessor are added to the assessment package and submitted to the accreditation body for technical review. The accreditation body will review all information submitted by the assessor and outcomes of the technical review in order to make the final accreditation decision.
The accreditation body assigns and schedules assessment activities to competent assessors so that the technical competence of the laboratory can be evaluated during the assessment. Laboratories can prepare for assessment activities by ensuring that applicable requirements are met in the performance of management and technical activities. The assessment process is used to demonstrate confidence in the competence of the laboratory.
ANAB Laboratory Accreditation
ANAB, the largest accreditation body in North America and leader in accreditation worldwide, provides accreditation to multiple standards in many industry-specific programs to ensure the competencies of laboratories. You can read more about ANAB Laboratory Accreditation here or Request a Quote here.