ASTM D1238-23: Melt Flow Rates Of Thermoplastics
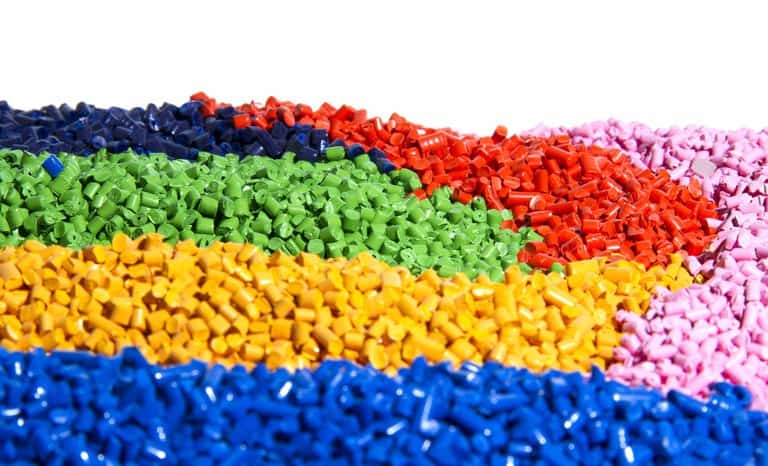
We use products made from thermoplastics every day. Drinking bottles, food storage containers, sports equipment, toys, plastic grocery bags, and shampoo bottles are all made from thermoplastics, which means these products can be melted down repeatedly and re-shaped into different forms. ASTM D1238-23: Standard Test Method For Melt Flow Rates Of Thermoplastics By Extrusion Plastometer details the test method used to determine the Melt Flow Index (MFI) and quality control tests on thermoplastics.
What Is ASTM D1238-23?
The test method in ASTM D1238-23 covers the determination of the rate of extrusion of molten thermoplastic resins using an extrusion plastometer. It is particularly useful for quality control tests on thermoplastics. The data produced by the test method serves to indicate the uniformity of the flow rate of the polymer as made by an individual process.
ASTM D1238-23 does not purport to address all of the safety concerns associated with its use. It is the responsibility of the user of the standard to establish appropriate safety, health, and environmental practices and determine the applicability of regulatory limitations prior to use.
Thermoplastics VS. Thermosets
There are two groups of plastic: thermoplastics and thermosets. Although they are both polymers, these materials behave differently when exposed to heat during the curing process. Thermoplastics do not form any chemical bond when curing, making them re-moldable and recyclable. Basically, thermoplastics are like wax: they can be molded and re-molded many times under the right temperature. Since they have a low melting point, they are ideal for applications that use recycled materials. For example, a foam cup is a thermoplastic material man be re-melted and fabricated into a dish. On the other hand, thermosets are able to withstand high temperatures without losing their shape, making them more durable. While thermosets strengthens when heated, this material cannot be remolded or heated after the initial forming.
The Test Method in ASTM D1238-23
Thermoplastic pellets soften when heated and become more fluid as more heat is administered. The test method in ASTM D1238-23 states that after a specified preheating time, thermoplastic resin is extruded through a die with a specified length and orifice diameter under prescribed conditions of temperature, load, and piston position in the barrel. The standard describes four procedures:
- Procedure A is used to determine the melt flow rate (MFR) of a thermoplastic material.
- Procedure B is an automatically timed measurement used to determine the melt flow rate (MFR) as well as the melt volume rate (MVR) of thermoplastic materials.
- Procedure C is an automatically timed measurement used to determine the melt flow rate (MFR) of polyolefin materials. It is generally used as an alternative to Procedure B on samples having melt flow rates greater than 75 g/10 min.
- Procedure D is a multi-weight test commonly referred to as a “Flow Rate Ratio” (FRR) test. Procedure D is designed to allow MFR determinations to be made using two or three different test loads (either increasing or decreasing the load during the test) on one charge of material.
What Are Common Thermoplastic Materials?
Commonly used thermoplastic materials include the following:
- Polycarbonate
- Acetal Copolymer Polyoxymethylene
- Acetal Homopolymer Polyoxymethylene
- Acrylic
- Nylon
- Polyethylene
- Polypropylene
- Polystyrene
- Polyvinyl chloride (PVC)
- Teflon
ASTM D1238-23: Standard Test Method For Melt Flow Rates Of Thermoplastics By Extrusion Plastometer is available on the ANSI Webstore.