Taking Flight: Why Thermal Altitude Testing Is Crucial for Success
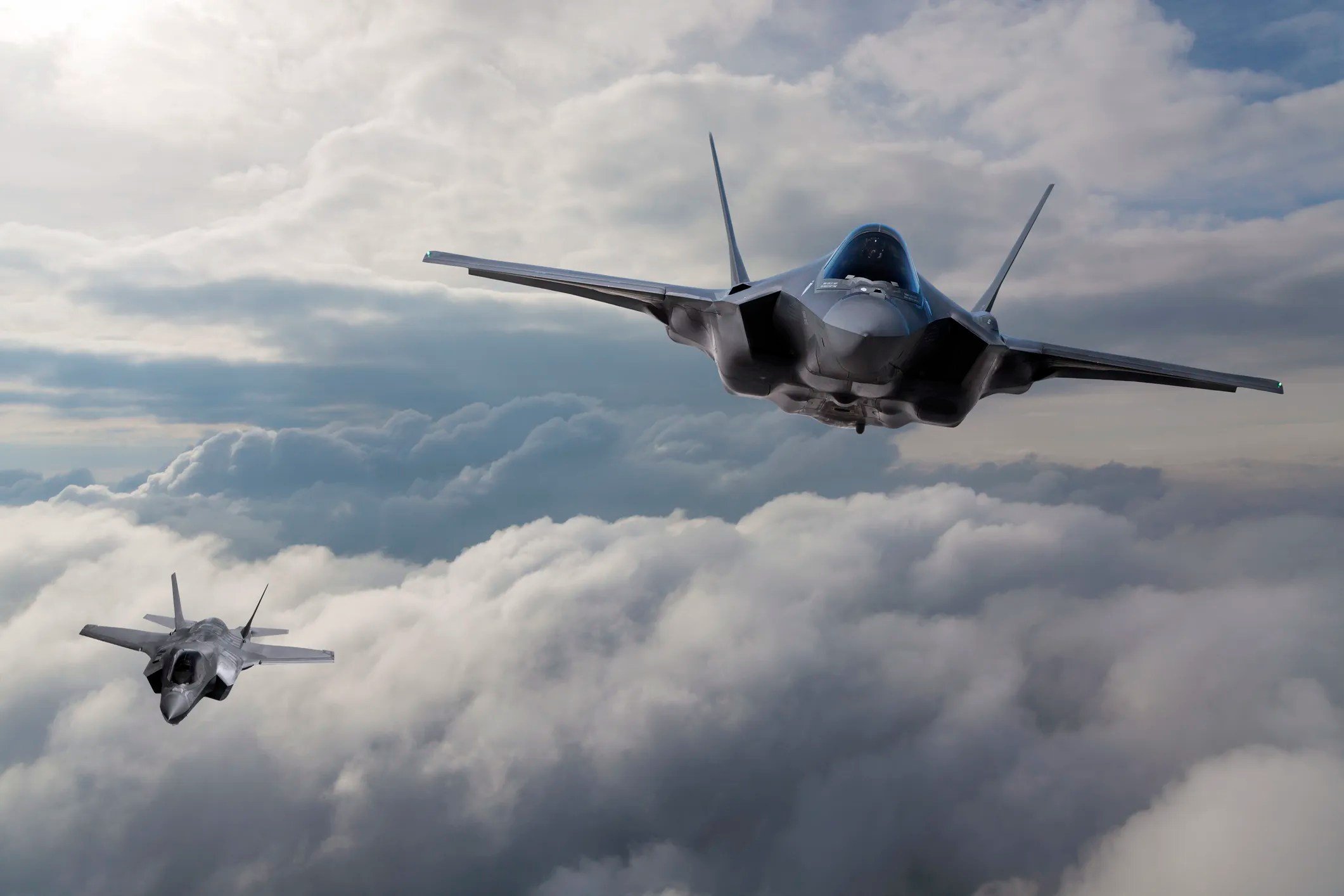
The journey of an aircraft, from the initial design phase to its triumphant takeoff, is a meticulous process filled with rigorous testing. One crucial aspect of ensuring a safe and successful flight is thermal altitude testing. Conducted within sophisticated chambers that replicate extreme environmental conditions, thermal altitude testing plays a vital role in evaluating the performance of flight hardware, components, and systems.
Understanding Thermal Altitude Testing
Imagine a chamber capable of mimicking the harsh realities of high-altitude flight. This is precisely what thermal altitude testing offers. By simulating the combined effects of extreme temperatures and low air pressure, these chambers create a rigorous testing ground for various flight-critical components. Temperatures ranging from a bone-chilling -80°F to a scorching 300°F are achievable within these chambers, pushing the limits of the equipment and revealing any potential weaknesses.
Another key aspect of thermal altitude testing is the ability to simulate the near-vacuum conditions encountered at high altitudes. These chambers can achieve pressures as low as 1.0 x 10^-8 torr, replicating the environment found hundreds of thousands of feet above sea level. This vacuum testing is essential for evaluating the performance of components that rely on specific pressure ranges to function properly. For instance, a faulty pressure sensor in a tactical control system at high altitude could have disastrous consequences.
These chambers can also simulate the varying air pressure conditions experienced throughout an aircraft’s ascent and descent. From replicating sea-level pressure to conditions found at a staggering 200,000 feet, these tests make sure that flight-critical systems can handle the rapid pressure changes encountered during a typical flight.
Why Thermal Altitude Testing Matters
The benefits of thermal altitude testing are far-reaching. By subjecting equipment to these extreme conditions, manufacturers can assure their products meet the stringent standards set by commercial aviation authorities, military specifications, and international regulations. This rigorous testing process helps maintain compliance and ultimately certifies that aircraft and space vehicles will perform as expected under the harsh realities of flight.
Perhaps the most crucial benefit lies in its ability to prevent potential problems before they occur. By identifying weaknesses in components during the testing phase, manufacturers can address any issues so their products are built to withstand the demanding conditions of flight. This proactive approach prevents adverse product reactions or unexpected equipment failures at critical moments during a flight, safeguarding the safety of passengers and crew.
The Mark of Excellence
Thermal altitude testing is a cornerstone of achieving the highest quality in aerospace engineering. By subjecting components to these rigorous simulations, manufacturers can deliver products and solutions that are reliable, durable, and built to perform flawlessly even under the most challenging flight conditions. Ultimately, it contributes to the overall safety and success of modern aviation. Interested in learning more about the intricate details of thermal altitude testing? The infographic below delves deeper into this crucial process, highlighting the specific environmental conditions simulated and the importance of testing for various industries. By understanding the science behind thermal altitude testing, we gain a greater appreciation for the meticulous steps taken to ensure the safety and success of every flight.
Contributing Author: Larry Rayhon, Senior Director of Product Engineering, Marotta Controls
Larry Rayhon is Senior Director of Product Engineering at Marotta Controls. For nearly 30 years, Rayhon has contributed to the success of key programs for customers and has recently taken the roll in leading all operations for Marotta’s power and actuation business unit. Joining Marotta in 1988, he spent 10 years leading the development group and transitioning many key programs from development to production.